
1988年,宁海的一家模具厂转行做笔筒,“得力文具”就此诞生。
从一只笔筒起家,到如今涉及40多个大类2000余种单品的雄厚家底,“得力”在中国文具综合实力排名中是当之无愧的“排头兵”。
一个“文具王国”崛起的背后,是一家传统的劳动密集型企业从生产方式到经营理念嬗变的转型之路。
突围:扭住技术革新这把利器
文具行业是典型的劳动密集型产业。2000年,“得力”跻身国内文具行业龙头企业之列,工业产值2.8亿元,员工近千人,到2007年,集团工业产值达到12.4亿元,员工人数则增加到4500人。相比于规模的扩张,企业人均产值几乎原地踏步。
与此同时,人力成本的快速增长和“用工荒”的频现,也让企业决策层倍感压力。“得力”开始寻求突围。
“传统意义上的劳动密集型产品,不一定要用劳动密集型方式生产,这是企业将来的出路。”总经理娄甫安将方向瞄准了生产方式的改变。
当时,“得力”曾与一厂家洽谈,希望通过合作开发,把多面贴标签的几道工序简化成一道全自动工序。结果,该厂家独自开发出了设备,并在行业内推广开来。
这一意想不到的变故,迫使“得力”投入力量自主研发。集团下属子公司“得力文具”率先成立技改小组,集团总部专设了一个技改办公室,高薪从广东聘请来4名工程师,打造一个20人的自动化研发团队。3年后,技改办升级为技改中心,集团常设技改人员也达到了80人。
今年,研发团队走访车间时发现,从韩国引进的三条固体胶流水线中,组装机成为限制产能的瓶颈。经过一番论证分析,公司决定自主研发一台组装机来更替。技改小组成员外出考察,跑技术展会,琢磨改进思路,终于从一台小型打孔设备上找到了灵感,成功开发新型组装机。
“测试下来,产能比原先提高了两倍,成本却节省了70%以上。”项目小组负责人欣喜地说,“有的车间原来有四五十个人,有了自动化装置后,人员减少到十分之一,产能反而提高了好几倍。”
据测算,自动化研发团队创建4年来,通过改装和研发生产设备,节约成本3000多万元。
几年前,“得力”还在上海成立了一支由20多人组成的研发中心,专门进行产品造型和功能开发。之后,负责颜色、图案等外观平面设计的另一个团队在韩国成立。凭借强大的研发能力,“得力”不断开拓办公和学生两大类文具产品,以每年一个多亿的产值增速,坐上国内综合文具头把交椅。
编辑: 徐挺纠错:171964650@qq.com
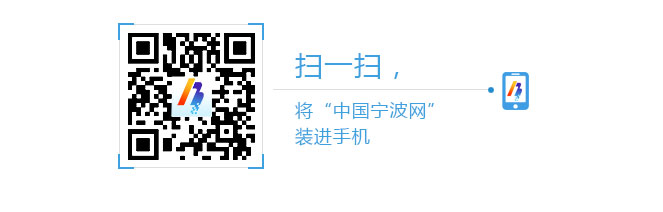