视频制作:马卫红
中国宁波网记者 李睿清 实习生 马卫红 通讯员 张佳婷
攻坚破难,合八条产线为一,提升产能利用率至96%;自主学习前沿技术,利用3D打印,将整车安装时间缩短至58秒……在位于前湾新区的上汽大众有限公司宁波分公司里,有这样一支成员平均年龄31岁的队伍——精益质量小组。他们不仅是今年全国工人先锋号的获得者,更是生产车间里的“六边形战士”。
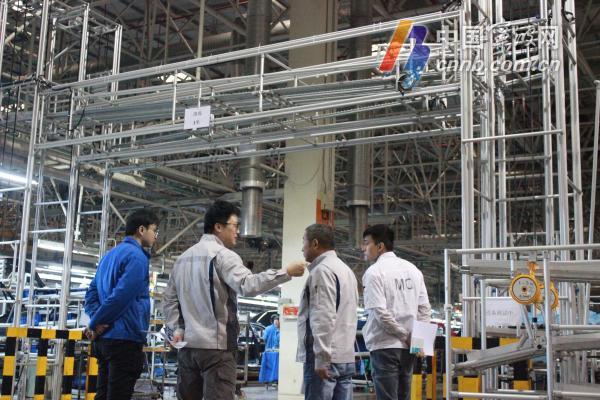
工作中的小组成员们。受访者本人供
小组于2017年成立,初衷是给当时刚起步不久的宁波分公司提供攻克难题、提升能效的生产力量,并为后续人才培养积攒经验。
作为攻坚主力,去年小组整了个“大活”——用4个月时间,将8种车型的生产整合至一条产线。此举不仅将产能利用率从71.5%提升至96%,还能在未来三年里节省成本近3亿元。
想实现“八线合一”不简单。8种车型,39种配置,超1万种零件要在一条产线上有序生产,还要保障合格率达98%。“国内目前较多的两线合一尚且需要8至12个月才能完成,八线合一的先例和经验在全世界都少有。”小组组长郑迪迪说,与此同时,小组还面临改造经费不足问题,想要完成这个目标,只能手动对产线拆解升级。
八种车型有大有小,想要在新产线上实现自动化生产,光重新设置操作标准就是难题。郑迪迪说,在底盘合装线上,因大小两种车型的质量相差一倍,底盘很难通过统一的惯性传送到合适的安装位置,生产效率始终提不上去。
解决方法不难,只需根据8种车型的质量重新设定刹车时间。但想找到其中的平衡点,却不容易。为此,整个小组耗时两个月,经过无数次计算、模拟、测试,最终在试验了近4万次后,找到了最佳制动位置。
此外,重新确定大小型号车身悬挂高度,也让小组犯过难。“车身和底盘合并时,需使用机械臂旋紧螺丝。但移线后,若仍对小型车使用大车型的车身悬挂高度,螺丝将无法旋紧,从而影响产品合格率。”郑迪迪说。
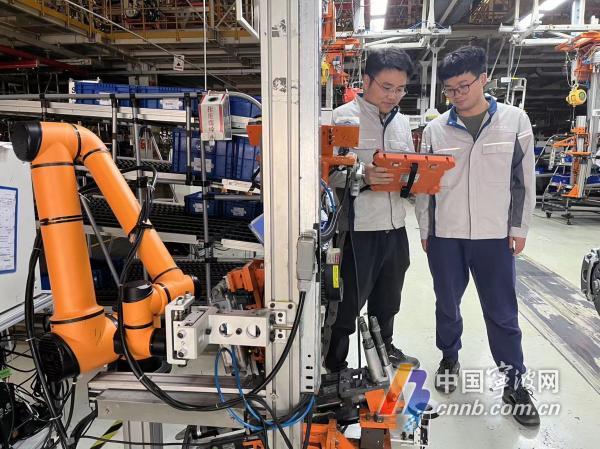
工作中的小组成员。受访者本人供
该怎么解决这个问题?小组将目光瞄准了3D打印。“早在2020年,我们就自主学习该技术,现在团队中已有3人具备专业水平。”郑迪迪说,通过自主设计图纸、建模等方式,小组仅用一周时间,就成功制作出合适的工装夹具,不仅将精度误差控制在正负0.5毫米内,还将整车安装时间缩短至58秒/台。
此外,小组还在日常工作中,发明了各式工具。使用3D打印技术制造的无线充电检测模块就是最好的案例之一,“市面上一个符合进入车间条件的检测手机至少上千元,而我们用3D打印的检测模块,在功能上与手机无异,但价格却低至十几元。”郑迪迪说。
如今,精益质量小组已走过7个年头,推动了1个自动化项目、6个数字化项目,总结出351条经验,并累计为企业降本1000余万元。“一个人能走得很快,但一群人能走得更远。接下来我们小组将继续为企业的降本增效、人员培养作贡献。”对未来,郑迪迪和组员们如此期许。
编辑: 陈晓怡纠错:171964650@qq.com