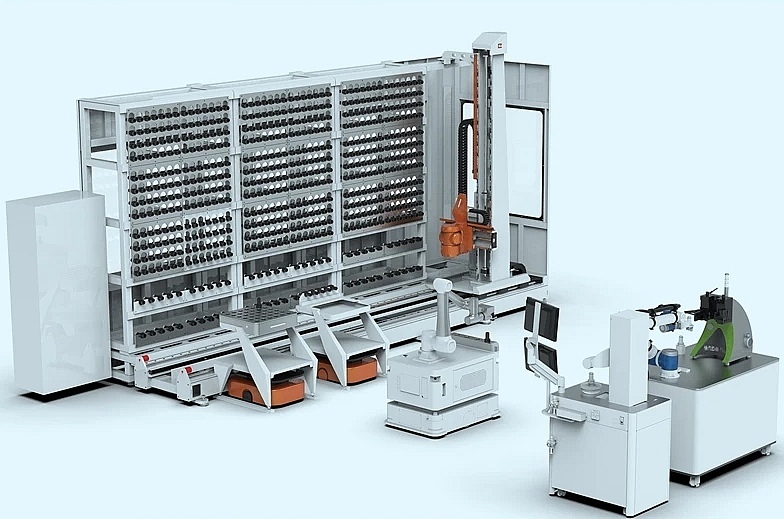
企业供图。
我是宁波伟立机器人科技股份有限公司研发的“全业务流刀具管理系统”,在机床轰鸣的工厂里,被称为“智造产线的刀具管家”。
刀具是机床加工过程中直接作用于工件的关键工具,主要用于切削、成型、钻孔、铣削等工艺,是制造业中高价值、高频消耗的核心耗材。
我的使命,是解决制造业产线上的一个痛点问题——对这些高价值却易损耗的“工业牙齿”进行管理。
传统模式下,刀具采购、调度、使用和报废分散在不同环节,数据断层、人工依赖度高,甚至可能因操作失误引发事故。但现在,我所掌握的射频识别技术追踪、全生命周期管理和智能动态调度三大“独门绝技”,可以有效解决这些问题。
我的核心能力,在于让每一把刀具都拥有“数字身份”。通过嵌入射频识别技术芯片或绑定条形码,刀具从入库那一刻起,刀柄、刀杆、夹头等部件的装配关系、使用次数、剩余寿命等数据,全部实时上传至我的数据库。
射频识别技术的原理很简单:每个芯片存储唯一编码,读写器通过无线电波获取信息,无需人工扫描即可批量识别。这让刀具流转效率提升数倍。
“过去工人需要手动记录刀具信息,现在系统自动追踪,误差率几乎为零。”使用过我的工厂管理者这样评价。
更厉害的是,我能根据加工任务自动匹配刀具组合。例如,面对多品种小批量订单时,系统会基于工艺需求,从数万把刀具中精准调取适配型号,并对寿命即将耗尽的刀具提前预警,避免加工中断。
如果说传统刀具管理是“头痛医头”,那我带来的则是“全生命周期”的革命。
我不仅打通了刀具库与机床的实时通信,还与客户的企业资源计划系统、制造执行系统深度融合。
当生产计划下达时,我能同步计算所需刀具数量、库存余量,甚至联动物流系统调配短缺刀具。而真正的智能化体现在动态策略上——我会根据刀具磨损数据、订单紧急程度、物流效率等因素,实时调整配送优先级。
“使用‘全业务流刀具管理系统’后,企业全年节省刀具成本300余万元,相当于实现了10%的效益提升。”我的价值被一家正在使用我的企业量化,这些数据让我倍感自豪。
我的能力源自伟立机器人团队在自动化领域20年的技术积累——他们对刀具崩刃、断刀、磨损不均等场景的深刻理解,被转化为软件系统与不同品牌机床“无障碍对话”的能力。
对于制造业而言,我的存在或许印证了一个趋势:在新质生产力的浪潮中,那些曾被视为“配角”的环节,正成为决定效率天花板的关键。甬派客户端宁波日报见习记者 林昱辰
编辑: 杜寅纠错:171964650@qq.com
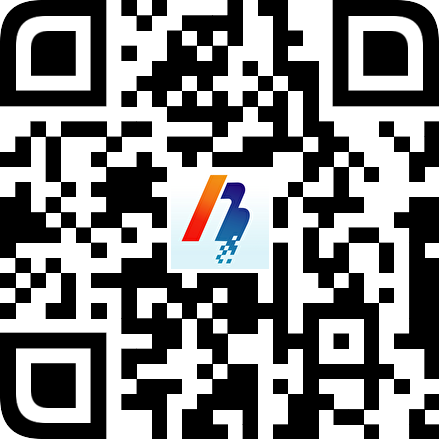
中国宁波网手机版

微信公众号